背景
お客様は韓国の大手化学企業であり、2000年代からベトナム市場に進出しています。長期的なビジョンと革新への取り組みのもと、生産最適化と品質向上のために研究開発投資(R&D)を重視しています。
昨年、同社は増加する需要に対応するため、生産ラインの拡張を目指しました。しかし、実施にあたり、次の3つの大きな課題に直面しました。
SCADAシステムの拡張性の問題
SCADAシステムは工場の生産活動全体を監視する中枢システムであり、数年前に別のベンダーによって導入されましたが、現在では技術資料が残っていません。これにより、以下のような問題が発生しました。
- 新規生産ライン用の制御インターフェースの修正が不可能
- 新たな監視・制御ポイントの追加が困難
- システム改修に伴うリスクが高い
老朽化したMESシステムがSCADAの拡張に対応できない
また、SCADAを拡張した場合、お客様が利用している老朽化した製造実行システム(MES)では接続や統合のニーズに対応できません。さらなる拡張を目指すには、SCADAとシームレスに統合し、リアルタイムでデータを提供できる最新のMESシステムが必要です。
材料計量プロセスを手作業で行っている
生産を拡大すると、計量が必要な材料の量も大幅に増えます。しかし、現在の計量プロセスは手作業で行われているため、データ入力に手間がかかり、ミスが発生しやすく、システムへの同期も難しくなります。これは、生産進捗の遅れや生産データの正確性への影響を引き起こします。上記の課題を解決し、運用を効率化しながらリスクを軽減するため、企業が材料計量プロセスを自動化し、データをSCADAやMES-Xに直接送信することが求められています。
ソリューション
得意分野であるIoT や生産自動化の経験を活かし、お客様の課題を迅速に把握し、最適なソリューションを提供しました。
SCADAとMES-Xの統合
ステップ1:SCADAシステムで課題を解決する。
SCADAは技術資料がありませんが、オープンシステムであるため、VTIは以下を実施しました。
- 技術的な分析を行い、システムの構成や仕組みを調査する。
- 現在のデータフローと通信方式を調査する。
- 拡大や新規の生産ラインとの連携が可能な箇所を特定する。
ステップ2:MES-Xシステムを展開する。
自社開発のMES-Xは、高い柔軟性を持ち、幅広い顧客ニーズに対応できるように設計されています。
- 生産管理用の標準モジュールが事前に統合されている。
- ニーズに応じてレイアウトやレポートをカスタマイズできる。
- 産業における様々な通信方式に対応できる。
- 品質およびトレサビリティ管理機能が搭載されている。
技術チームは化学製品の製造プロセスに特化するため、複数の機能を調整しました。
ステップ3:2つのシステムを統合する。
- SCADAの機能拡張:生産ラインの新規制御画面レイアウトを設計し、SCADAを新規生産ラインのPLCと連携して制御および監視機能を拡張する。
- SCADAとMES-Xの中間のデータアーキテクチャへの同期:両システムがリアルタイムでデータを読み書きし、共有できる中間データベースを構築することで、データの同期とデータフローの最適化を確保する。
IoT サービス活用でのデータ収集の自動化
IoT サービスの導入により、計量器からデータを直接収集し、SCADAシステムへ送信してLANネットワークを通じて既存のデータタグをMES-Xに同期させることで、情報をリアルタイムで自動的に更新できる。
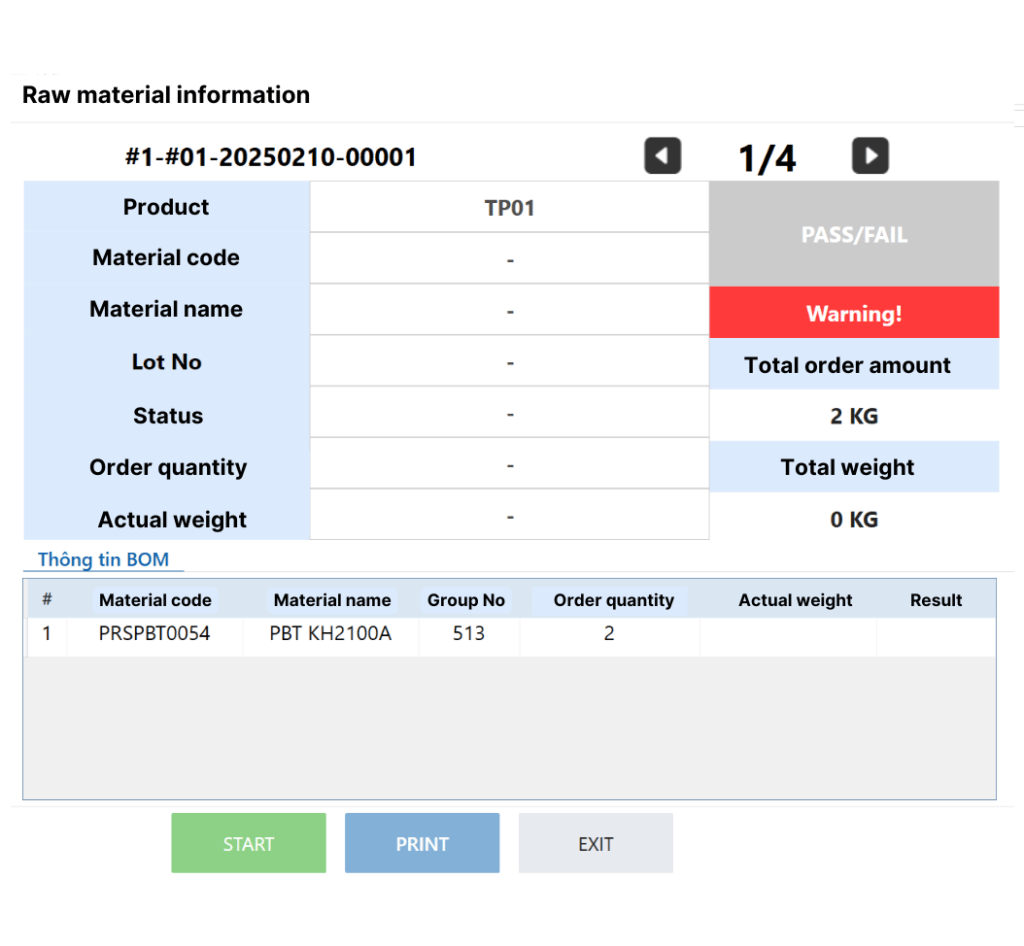

成果
VTIが導入したソリューションにより、お客様は次のような成果を得ることができました。
- 新規の生産ラインのデータがすべてSCADAに同期され、生産の監視・制御がさらにスムーズになりました。
- MES-Xが安定して稼働し、SCADAとシームレスに統合されることで、データ通信の迅速化と正確性を実現しました。
- 材料計量プロセスを自動化することで、手作業によるミスを減らし、運用効率を向上しました。
まとめ