Retail is changing faster than ever. While some businesses still count inventory by hand and update spreadsheets manually, the most successful retailers have discovered a game-changing secret: automated inventory management systems.
The demand for automated inventory management is skyrocketing. The global inventory management software market reached an estimated $3.58 billion in 2024 and is forecast to double to over $7 billion by 2033, with an annual growth rate of around 8 – 9%.
In the Asia Pacific region, the market is growing even quicker, with annual growth rates reported as high as 10 – 12% as digital transformation accelerates across countries like Singapore and Vietnam.
In this guide, we’ll explore how automated inventory management can transform your business operations, dramatically improve accuracy, and help you stay competitive in the digital age.
What is Automated Inventory Management?
Automated inventory management refers to the use of technology – such as specialized software, barcode scanners, and RFID tags – to track, update, and control inventory with minimal human intervention.
Think of it as having a super-smart assistant that never sleeps, never makes calculation errors, and can track thousands of products across multiple locations simultaneously.
Why Should Manual Inventory Be Replaced by Smart Methods?
With traditional inventory management methods, you’d need to manually count every smartphone, laptop, and accessory in your store, which can be time-consuming and prone to error. After counting, you’d have to update spreadsheets by hand, leaving room for mistakes and inconsistencies.
Reordering stock would often rely on memory or rough estimates rather than actual data, forcing you to guess when it’s time to restock. As a result, you’d constantly be hoping that your calculations are accurate – otherwise, you risk overstocking or running out of popular items.
Consider these eye-opening statistics: The average retail business relying on manual tracking achieves just 66% inventory accuracy. That means one-third of your inventory data is wrong at any given time. Imagine if your bank account balance was wrong 34% of the time – you’d switch banks immediately!
Meanwhile, businesses using automated systems achieve 97% accuracy. That’s not just an improvement – it’s a transformation.
Human error is responsible for costly mistakes in nearly 43% of warehouses globally. Every miscounted item, every forgotten reorder, every data entry mistake adds up to real money lost. Smart inventory systems eliminate these human errors, replacing them with consistent, reliable automation.
Core Components & Functionalities
Modern automated inventory management systems work like a well-orchestrated symphony, with each component playing its part to create harmony in your operations.
Component | Purpose |
Inventory Management Software | Real-time tracking and central database |
Automated Replenishment | Auto order generation and stock optimization |
Barcode/RFID Scanning | Fast, accurate item tracking and data entry |
Cloud/Mobile Integration | Anywhere access and workflow flexibility |
Multi-location Tracking | Unified oversight of inventory across multiple sites |
System Integration | POS/eCommerce/ERP/WMS connection |
Data Analytics & Reporting | Actionable insights and forecasting |
User Interface & Access Control | Efficient operation and security |
Automated Alerts | Real-time notifications for key inventory events |
5 Benefits of Automated Inventory Management
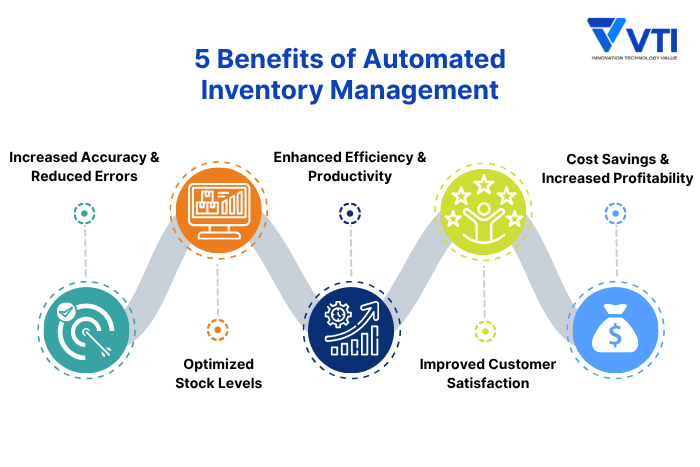
Dramatically Increased Accuracy & Reduced Errors
The transformation is immediate and measurable. Inventory accuracy rises from 66% with manual methods to 97% with automation via RFID tags. This isn’t just about numbers – it’s about trust.
When customers ask if you have something in stock, you can answer with confidence. When you make purchasing decisions, you’re working with accurate data. The elimination of manual data entry mistakes means better data integrity and fewer costly discrepancies between physical and digital stock.
Optimized Stock Levels (No More Stockouts or Overstocking)
Here’s a staggering statistic: stockouts cause up to $1 trillion in missed sales annually worldwide. Automated systems prevent this catastrophe through accurate demand forecasting and automated reorder points.
On the flip side, overstocking can inflate storage costs by 20-30%. Smart inventory systems find the sweet spot – maintaining optimal stock levels that prevent both shortages and excess inventory. This means improved cash flow as less capital is tied up in unsold goods.
Enhanced Efficiency & Productivity
Time is money, and automated systems give you both. These systems can save up to 95% of the time spent on manual data entry, freeing up your staff for higher-value activities like customer service, strategic planning, and business development.
The streamlined warehouse operations – from picking to packing to shipping – mean faster turnaround times and happier customers. Your team can focus on growing the business instead of counting inventory.
Improved Customer Satisfaction
Customer expectations are higher than ever. With 69% of online shoppers abandoning purchases when items are out of stock, accurate inventory management directly impacts your bottom line.
Automated systems ensure faster, more reliable fulfillment, consistently accurate inventory data for customer queries, and reliable delivery times. The result? Fewer negative reviews and more repeat customers.
Cost Savings & Increased Profitability
The financial benefits extend far beyond labor savings. Automated systems reduce carrying costs, minimize losses due to spoilage and obsolescence, and virtually eliminate theft-related inventory shrinkage.
Most importantly, companies with optimized inventory systems see up to 30% better order fulfillment rates and improved sales growth. When you can reliably fulfill orders, satisfy customers, and operate efficiently, profitability naturally follows.
9 Key Features to Look for in an Automated Inventory Management System
When evaluating automated inventory management systems, think of yourself as assembling a championship team – each feature needs to contribute to your overall success. Let’s dive deep into the essential features that separate good systems from great ones.
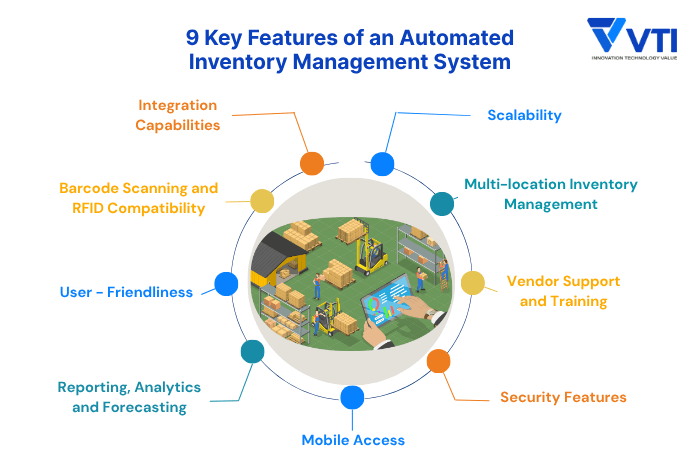
Integration Capabilities
Think of integration as the nervous system of your business operations. A truly effective automated inventory system doesn’t work in isolation – it becomes the central hub connecting all your business applications.
When evaluating integration capabilities, it is important to look for features such as two-way data synchronization with your existing CRM, ERP, e-commerce platforms, and accounting software.
The system should also offer API flexibility to support custom integrations as your business evolves, along with real-time data flow that ensures updates occur simultaneously across all platforms.
Scalability
Scalability in an inventory management system is about more than just accommodating a growing volume of products – it’s about adapting seamlessly to your business’s evolving needs without requiring a complete system overhaul.
A scalable system should manage increased volume effortlessly, support the addition of advanced features, function across multiple time zones and currencies, and allow smooth user expansion with role-based permissions. Avoid systems with restrictive limits or rising costs tied to usage spikes, as they can hinder long-term growth.
User-Friendliness
The most sophisticated system fails if your team can’t use it effectively. User-friendliness extends beyond a pretty interface – it’s about matching your team’s workflow and capabilities.
A user-friendly platform should align with team workflows, enabling users to complete tasks with minimal training. Features like role-specific dashboards, mobile-friendly interfaces, and intuitive navigation streamline day-to-day operations and shorten the learning curve. Systems that support localized training materials and cater to varying technical skill levels will foster wider acceptance and reduce onboarding time.
Reporting, Analytics, and Forecasting
Effective reporting and analytics are vital components of a high-performing inventory management system, turning raw data into meaningful insights that drive smarter business decisions.
The system should turn raw data into clear insights through real-time dashboards, customizable reports, and automated alerts for issues such as low stock or overstocks. Advanced analytics tools can reveal trends, track supplier performance, and even break down profitability by product, category, or location.
Predictive modeling enhances this by forecasting future demand using seasonal trends, external factors, and historical data – helping businesses reduce stockouts and minimize excess inventory.
Mobile Access
Modern business moves too fast to be tied to a desktop computer, making mobile access essential for responsive inventory management.
Modern inventory systems must allow full access from smartphones or tablets, offering real-time updates, barcode scanning, and even offline functionality in low-connectivity areas. This mobility empowers staff on the warehouse floor, at remote sites, or on the move to make informed decisions without delay.
Security Features
Your inventory data represents significant business value and requires enterprise-grade protection to keep it safe.
With so much sensitive business data at stake, the system must include features like encryption, multi-factor authentication, and role-based access control. Audit trails and compliance with local and international regulations – such as GDPR or country-specific data residency rules – help protect the business and build trust with customers.
Vendor Support and Training
The relationship with your vendor extends far beyond the initial purchase, as comprehensive support ensures your system continues delivering value as your business evolves.
A reliable provider offers more than initial setup – they provide timely assistance, regular software updates, and continuous training as your system evolves. Local language support, structured onboarding for new staff, and a responsive customer service team are vital. A good vendor also adapts to your changing needs and keeps the system aligned with your business goals.
Multi-location Inventory Management
As your business expands across multiple locations, centralized inventory management becomes crucial for maintaining efficiency and consistency.
A capable system should synchronize inventory data across locations in real time, support inter-location transfers, and allow for location-specific pricing and promotions. More advanced features, such as cross-docking or regional supplier management, ensure operational efficiency as the network grows.
Barcode Scanning and RFID Compatibility
These technologies form the backbone of accurate inventory tracking, but implementation details matter significantly.
Systems should support various barcode types, custom labeling, and batch scanning for faster processes. RFID integration allows bulk, non-line-of-sight scanning and real-time item tracking – boosting accuracy significantly and reducing labor costs. Many businesses that implement RFID report improved accuracy levels of up to 97%, with the investment typically recouped within a year.
Top 7 Automated Inventory Management Software Vendors
For businesses of all sizes, efficient inventory management is crucial for success. The right inventory management system can streamline operations, reduce costs, and improve customer satisfaction. Here’s a closer look at some leading smart inventory management solutions, each with its unique strengths and ideal user base:
VTI
VTI is a technology company with a strong presence in the Asia-Pacific (APAC) region, specializing in cloud-based, scalable inventory and procurement management. Their inventory management offerings are tailored to address the specific needs and challenges faced by businesses operating within this dynamic market.
VTI’s key features include real-time inventory tracking with advanced forecasting capabilities, supplier management tools, and automated stock replenishment. The platform is built on a cloud-based infrastructure using AWS, ensuring high scalability and performance. It also offers deep integration with ERP and financial systems, along with automation capabilities that can reduce procurement-related workloads by up to 50%.
Their proven experience in inventory management for Japanese retailers enhances their value for companies needing an end-to-end IT service for advanced inventory management systems across the Asia-Pacific market.
NetSuite (by Oracle)
As a cloud-based suite of applications, NetSuite is a powerful enterprise resource planning (ERP) system that offers a wide range of functionalities beyond just inventory management.
NetSuite stands out for large enterprises seeking comprehensive ERP solutions. Its strength lies in combining inventory, financials, and business operations in one centralized inventory platform. This holistic approach allows large organizations to gain complete visibility and control over their entire business processes.
However, the inherent complexity of such a vast system and its associated cost may overwhelm smaller businesses that do not require its full breadth of features.
Zoho Inventory
Part of the broader Zoho suite of business applications, Zoho Inventory is a cloud-based inventory management system specifically designed to help businesses efficiently track their stock, manage orders, and streamline their sales processes.
Zoho Inventory excels for small to medium businesses (SMBs) with its affordable pricing and multi-channel selling capabilities. Its automated reordering and integration features provide excellent value, helping SMBs optimize their stock levels and avoid stockouts.
While it offers robust features for its target market, scalability limitations may require businesses experiencing rapid growth to consider alternative solutions or upgrades in the future.
Cin7
Cin7 is a comprehensive inventory and order management software solution that caters specifically to product-based businesses, particularly those involved in retail, wholesale, and online sales. It aims to provide an all-in-one platform for managing inventory across various sales channels.
Cin7 serves retailers and wholesalers with comprehensive Point of Sale (POS), inventory, warehouse, and B2B eCommerce integration. Its omnichannel strength allows businesses to manage their inventory and sales seamlessly across multiple touchpoints.
However, this robust functionality comes with a steep learning curve that often requires dedicated training time for users to fully leverage its capabilities.
TradeGecko (now QuickBooks Commerce)
Originally known as TradeGecko, this platform was acquired by Intuit and rebranded as QuickBooks Commerce. It is an inventory and order management solution primarily aimed at small to medium-sized online businesses looking to streamline their e-commerce operations.
Its ease of implementation makes it an attractive option for businesses looking to quickly get started with managing their online inventory. While user-friendly, it’s primarily focused on eCommerce applications, which might limit its suitability for businesses with more complex brick-and-mortar or manufacturing needs.
Fishbowl Inventory
Fishbowl Inventory is a popular smart inventory management system that integrates seamlessly with QuickBooks, making it a strong contender for businesses already using QuickBooks for their accounting needs. It’s particularly well-suited for manufacturing and warehouse environments.
However, users might find that the interface feels dated compared to newer, more modern inventory solutions available on the market.
inFlow Inventory
inFlow Inventory is an intuitive inventory software designed primarily for small businesses with easy invoicing, stock control, and B2B portal features. Its simplicity and straightforward functionality make it an excellent choice for smaller operations looking for a basic yet effective inventory management system.
However, its enterprise-level features are limited, meaning it may not be suitable for larger businesses with complex inventory needs or extensive supply chains.
Implementing Automated Inventory Management: A Step-by-Step Guide
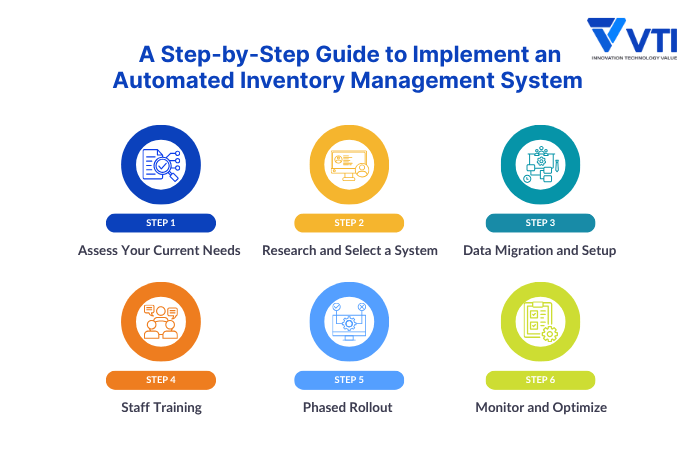
Successfully implementing automated inventory management requires a methodical approach, much like building a house – you need a solid foundation before adding the finishing touches.
Step 1: Assess Your Current Needs
Begin by mapping out your current workflow and identifying specific pain points. Are you struggling with stockouts, overstocking, or inaccurate data? Document these challenges to ensure your new system addresses real problems.
Step 2: Research and Select a System
Compare vendors systematically, request demos, and check reviews from businesses similar to yours. Don’t rush this decision – the right system will serve you for years.
Step 3: Data Migration and Setup
Cleanse and import your current inventory data carefully. This step often reveals data quality issues that need addressing before going live.
Step 4: Staff Training
Ensure your team is comfortable using the new system through comprehensive training. Change management is crucial for successful adoption.
Step 5: Phased Rollout
Test the new system with a small segment before full adoption. This approach allows you to identify and resolve issues without disrupting your entire operation.
Step 6: Monitor and Optimize
Continuously track performance metrics and make adjustments for ongoing improvement. Your system should evolve with your business needs.
Conclusion
The transformation from manual to automated inventory management isn’t just about technology. It’s about positioning your business for sustained success in an increasingly competitive marketplace.
As we’ve seen throughout this guide, businesses that embrace automation achieve remarkable improvements: accuracy jumps from 66% to 97%, costs decrease significantly, and customer satisfaction soars. Companies like VTI are helping retailers across Asia-Pacific realize these benefits through tailored solutions that understand regional business needs.
The question isn’t whether you can afford to implement automated inventory management – it’s whether you can afford not to. Every day you delay means lost sales, frustrated customers, and competitive disadvantage.
Your journey toward inventory automation starts with a single step: evaluating your current systems and envisioning what’s possible. The tools, technology, and expertise exist today to transform your operations.
Ready to streamline your inventory and transform your business? Contact VTI today to discover how our automated inventory management solutions can help you achieve higher accuracy, reduce costs, and delight your customers.
Contact us now