Client Background & Requirements
Our client specializes in construction machinery, mainly concrete spraying vehicles. Traditionally, these machines were manually operated—workers used a handheld controller to control the spraying process.
However, manual operation often leads to inconsistencies, such as uneven concrete distribution and incomplete spray coverage. To enhance precision and reduce human error, the client aims to automate the spraying process, which includes:
- 3D Workspace Mapping – A high-precision digital modeling system to capture and map the work environment, enabling accurate automated operations across complex construction spaces.
- Smart Control System – An intelligent automation system for real-time adjustment of critical spraying parameters (angles, pressure, and nozzle positioning), ensuring uniform concrete coverage across irregular surfaces where manual operation often falls short.
Our Solution
3D Workspace Mapping: Advanced Digital Environment Scanning
A significant challenge in automating the spraying process is achieving precise navigation and positioning in complex tunnel environments. VTI addressed this by developing a 3D Workspace Mapping system, enabling the machine to operate with millimeter-level accuracy.
- LIDAR Sensor & Total Station Machine:
- The LIDAR sensor continuously scans the environment using laser pulses, generating real-time 3D point cloud data of the tunnel’s structure.
- The Total Station Machine enhances localization by precisely tracking the machine’s position within the tunnel coordinate system.
- Windows PC: Runs on software to collect and process Point Cloud data from LIDAR and determine precise vehicle coordinates via the Total Station Machine.
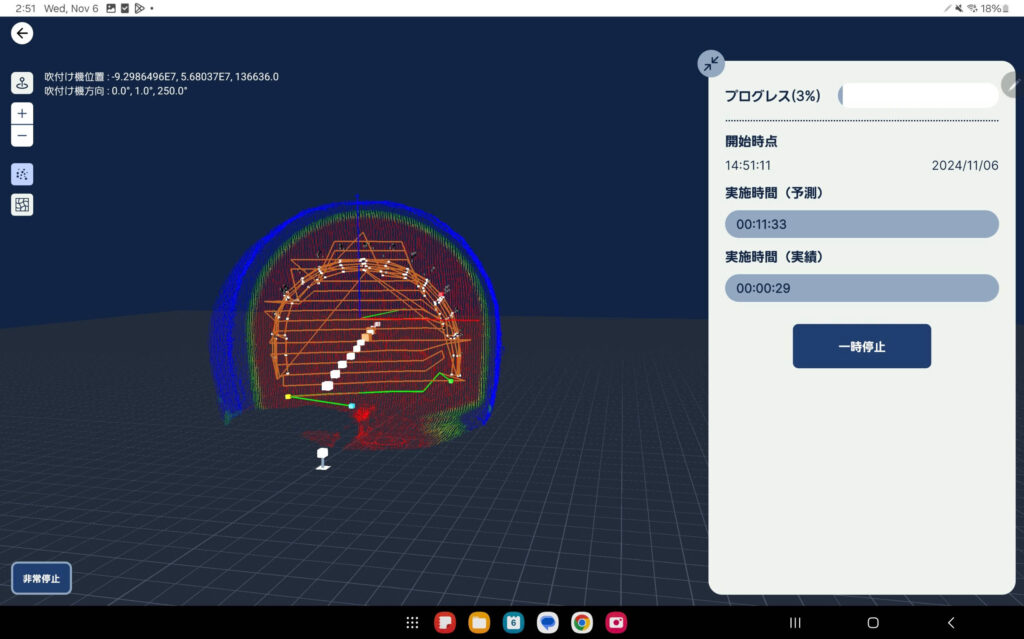
Smart Control System: Comprehensive Interactive Control Solution
The Smart Control System ensures precise, automated control by integrating several hardware components: real-time sensor feedback, IPC, Controller, ….
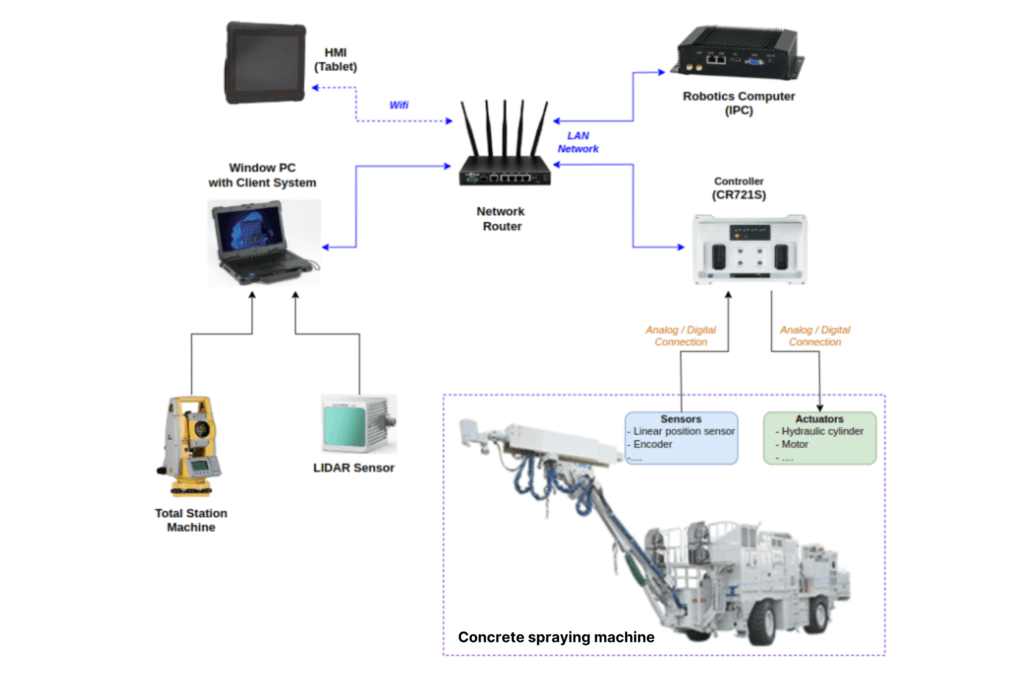
The system starts with a tablet-based HMI, where operators can either manually control the machine or define an automated spraying process. Once set, the Robotics Computer uses 3D Workspace Mapping on PC as the source of data to optimize movement based on real-world conditions. Historical data further refines spray paths, reducing unnecessary movements and ensuring full coverage.
During execution, the Controller continuously receives optimized movement commands, activates actuators, and makes real-time corrections using sensor feedback. This prevents overspraying, material waste, and inconsistencies, leading to a more efficient and cost-effective operation.
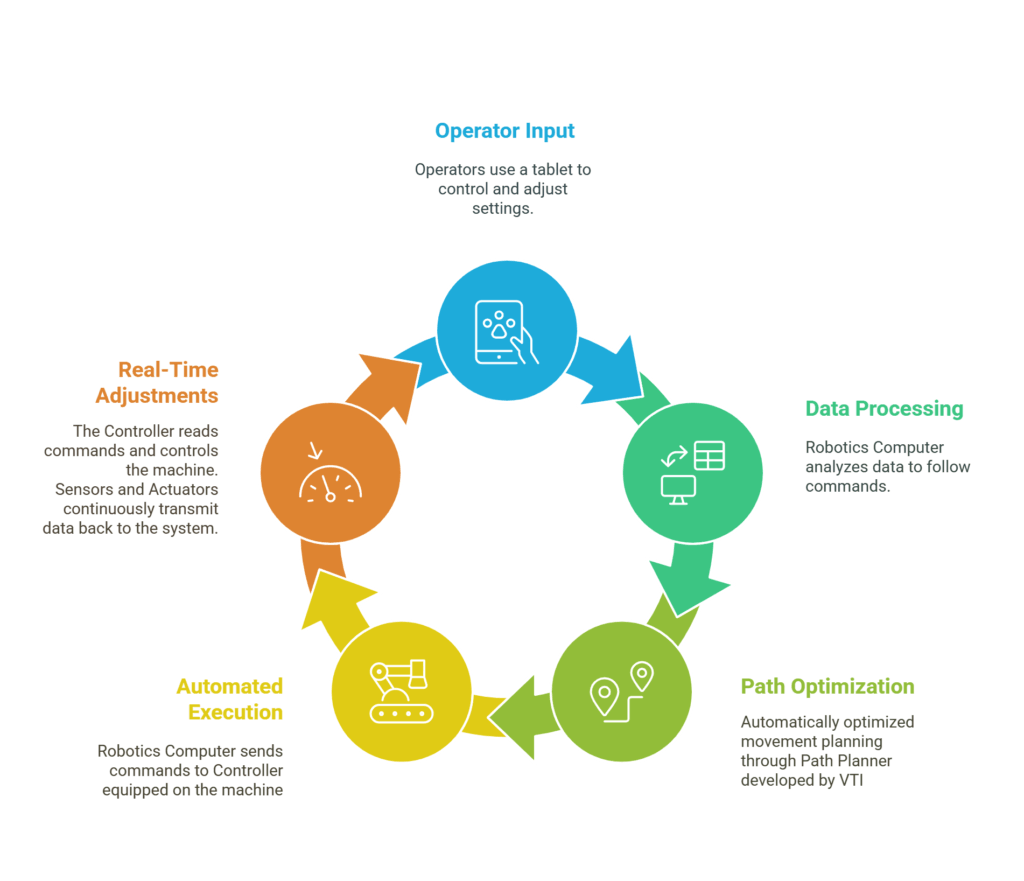
By integrating 3D Workspace Mapping and the Smart Control System, VTI has transformed manual spraying into a fully automated and intelligent process, ensuring precision and efficiency while allowing manual control when necessary.
All components are seamlessly connected within a unified LAN network, forming a comprehensive IoT system that enables real-time data exchange, synchronized operations, and enhanced automation.
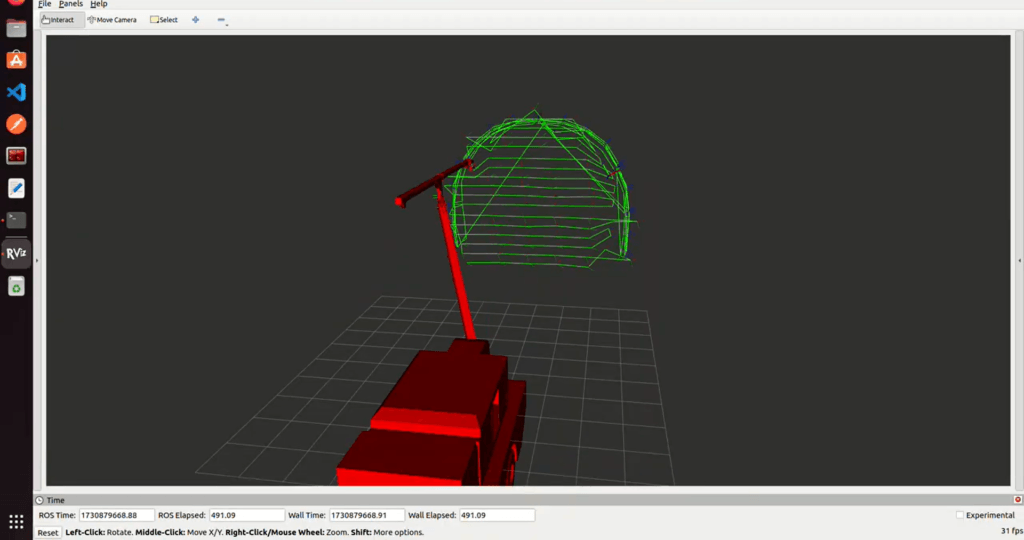
Project Technology
HMI:
– OS: Android
– Programming Language: Java/Kotlin, Flutter
Robotics Computer
– OS: Ubuntu
– Framework: Robot Operating System (ROS)
– Programming Language: C++, Python
Maximize Your Business Potential with Our IoT Services
This success story demonstrates our expertise in delivering tailored IoT solutions that address complex challenges and perfectly align with your business needs.
Our strength lies in our unique ability to bridge advanced programming capabilities with industrial automation expertise, delivering comprehensive solutions of IoT networks that elevate manufacturing operations to unprecedented levels of efficiency and automation.
Contact us today to explore our cutting-edge IoT solutions!