This blog introduces a tailored IoT solution delivered by VTI that unified diverse CNC machines, boosting performance, reducing downtime, and enabling smart factory operations.
Client Overview
Our client is a leading Japanese FDI company specializing in pneumatic and industrial automation equipment. Operating in Vietnam since the early 2000s, they manage two large-scale manufacturing plants covering 600,000 m², positioning themselves among the top pneumatic equipment manufacturers in the region.
Challenges
The client operates hundreds of CNC machines from eight different suppliers, creating a fragmented ecosystem with varied designs and data accessibility: Some machines are closed systems with no data extraction capability, others use PLCs, and some already integrate monitoring software but lack a unified management solution.
As a result, the client required a solution that could seamlessly connect all CNC machines, collect and synchronize critical data, including:
- Operational Status: Track machine uptime and downtime and detect real-time failures.
- Predictive Maintenance: Monitor runtime data to optimize maintenance schedules.
- Overall Equipment Efficiency (OEE): Assess individual machine performance, optimize workload distribution, and maximize productivity.
All collected data would be integrated into MES-X, our advanced Manufacturing Execution System, enabling a unified, data-driven approach to factory management.
Comprehensive IoT Solution
VTI conducted an on-site assessment to determine the connectivity potential of each machine type. Based on this, machines were categorized into three groups, each requiring tailored IoT solutions:
Closed System Machines
For machines with no external data access, VTI deployed Remote I/O devices to read electrical signals from indicator lights, determining machine status:
- Operating status: Run – Stop
- Error status: NORMAL – WARNING – ERROR
A relay-based interface ensured seamless integration without interfering with machine operations or causing signal disruption.
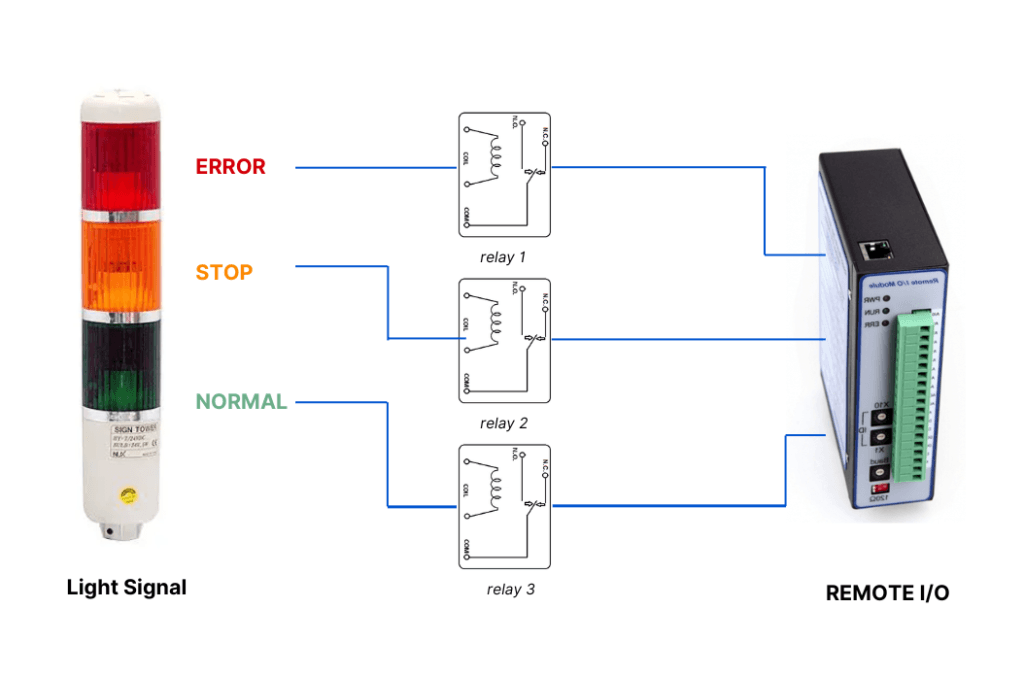
PLC-Controlled Machines
IoT Gateways were installed to connect with PLCs via industrial protocols like CC-Link, OPC UA, and Modbus. Data was extracted directly from PLC and transmitted to IoT Edge Servers over a LAN network.
Machines with Built-in Monitoring Software
IoT services were developed on IoT Edge Servers to extract data from existing monitoring software using various methods, including log file parsing, database queries, and REST API integration, etc.
Overall IoT System Architecture
The IoT Edge Server plays the central role that collects data from Remote I/O, IoT Gateways, and monitoring systems. It converts everything to a standard format, stores it locally, and sends the processed data to the MES-X Server.
We installed IoT Edge Servers in every workshop to store data locally. This keeps operations running smoothly even during network disruptions, as data is stored on-site and automatically uploaded when the connection is restored.
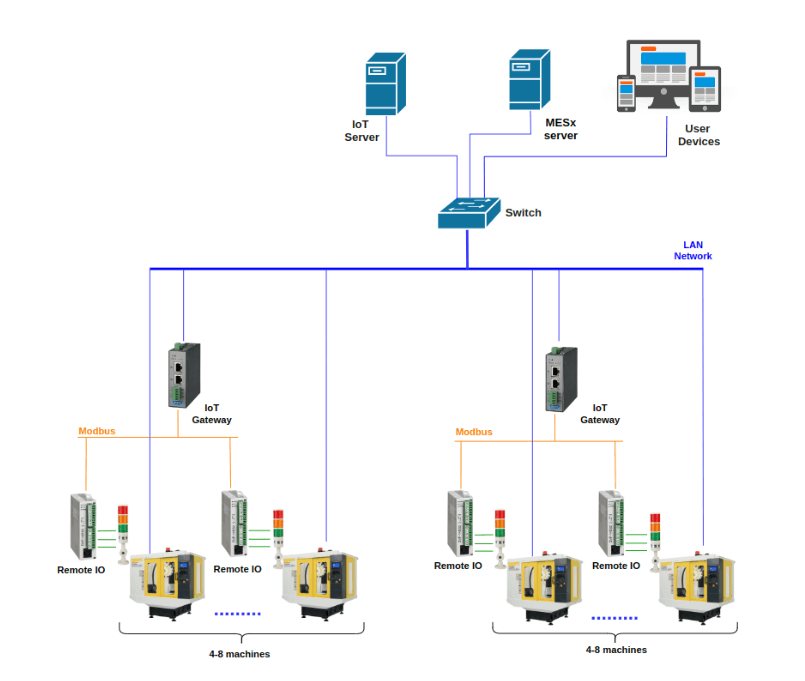
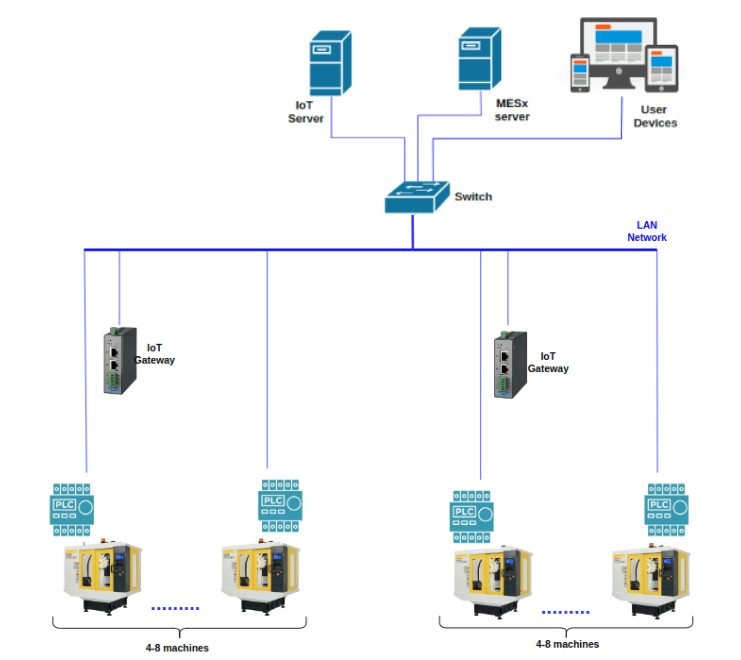
Data from all three machine groups is collected and synchronized into the MES-X system for status monitoring, performance optimization, and maintenance support.
Results
Implementing this comprehensive IoT solution delivered significant improvements:
- 13% reduction in machine downtime – Faster issue detection and optimized production scheduling.
- 12% reduction in maintenance costs – The data-driven maintenance schedule prevents unexpected failures.
- 16% increase in machine utilization – Real-time OEE insights optimize workload distribution.
- Reliable and seamless operation – IoT Edge Servers ensure continuous data availability, even during network failures.
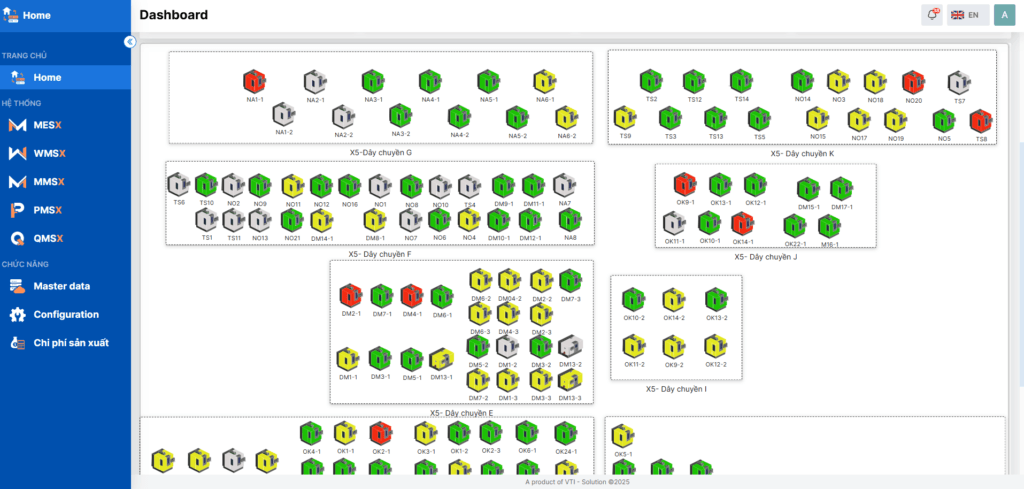
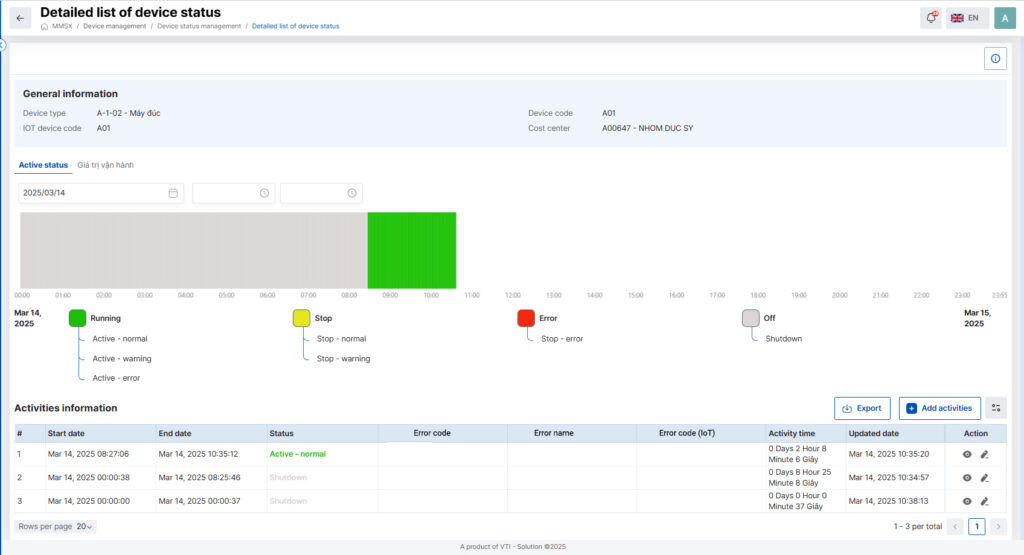
Conclusion
VTI delivers tailored, end-to-end IoT solutions that empower manufacturers to digitally transform production, improve maintenance efficiency, and optimize overall operations. Our expertise seamlessly integrates diverse machine ecosystems, automates data collection, and synchronizes critical insights—creating a manufacturing environment that’s both efficient today and prepared for tomorrow’s challenges.
Ready to elevate your factory’s efficiency? Contact VTI today to explore our IoT solutions!